Precise Location Tracking is the Key to Complete Chain of Custody
- Team Deeyook
- Jul 3, 2023
- 5 min read
Updated: Apr 24, 2024
This blog is based on a webinar given by Deeyook Founder and CEO, Gideon Rottem. To watch the webinar, click here.
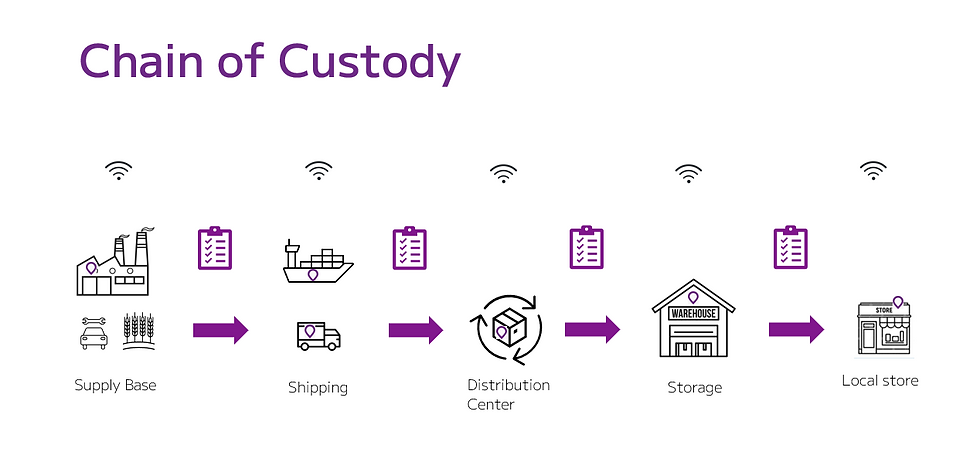
The supply chain disruptions and delays that have been plaguing manufacturers across industries for a number of years grew significantly worse during the Covid-19 pandemic. Even as the pandemic has waned, the disruptions continue, and a 2022 survey revealed two-thirds of Fortune 2000 companies reporting losses of up to 15% due to supply chain disruptions.
Supply chain disruptions can be caused by any number of reasons - from part shortages to shipping delays to defective items. If just one component is not where it’s meant to be at a particular time, there can be a snowball effect causing delays down the production line and putting a significant dent in productivity and profitability.
To get this visibility, companies need to maintain a complete chain of custody of each item that moves between parties in the supply chain. Accurate and precise location tracking is the key to ensuring that each and every item is always accounted for, no matter where it is.
Supply Chain Risks
The exact supply chain for each product is different and can range from simple, with one or two links in the chain, to very complex, with a whole maze of distribution centers and multiple modes of transportation.
While an asset is on its supply chain journey, it is subject to a number of risks that can impact overall productivity and efficiency, including:
Physical security risks - an item can break or get lost.
Inaccurate or insufficient data - deadlines can be missed if manufacturers are given wrong information as to when an essential part will be arriving, holding up the entire production line.
Lack of standardization - defective parts can prevent orders from being fulfilled on time.
Poor integration and communication - planning can be difficult if not everyone has access to the most updated information.
Human errors - while it’s natural for everyone to make mistakes, if someone misplaces a part or manually enters wrong information, there can be lasting repercussions.
Scalability and infrastructure challenges - when dealing with large amounts of inventory, it can be very hard to keep track of it all manually.
These risks happen because, throughout the supply chain, items are moving from place to place. Whether it’s a component that has to get from a factory in one country to another or a completed product that has to end up in hundreds of different retail locations, there are many moving parts at all times. Every time an item is on the move, it is vulnerable to disruption.
What seems like one small disruption can have a huge ripple effect - in fact, a single 30 day production stoppage can cost a company 30-50% of its EBITDA. In recent years, the pharma industry lost $60 billion and the automotive industry lost $45 billion due to supply chain disruptions. Industries cannot afford these huge losses, and the good news is that there is a solution.
How Chain of Custody Helps
The term chain of custody refers to the process of following material and assets through each step of the supply chain - from sourcing to production to shipping to retail stores or home delivery. At every step of the way, there is clear visibility into the ownership, custody and location of each item.
Currently, 75% of companies manage their chain of custody manually. Fortunately, this is starting to change as more companies are embracing the digital transformation and are adopting technological tools enabling them to collect more information faster and more accurately. With better visibility into the chain of custody, companies can act faster to address challenges, keep customers more informed, and avoid many of the potential pitfalls that lead to supply chain disruptions.
Overall, maintaining a chain of custody provides the following benefits:
Clear visibility into where all assets are at all times.
Better process efficiency and lower TCO.
Safety compliance.
Elimination of theft or loss of goods.
Regulatory compliance.
It’s All About Location
Obviously, a huge part of the chain of custody is knowing exactly where an item is at any given time. This is especially important in the pharma and food industries where it can be a matter of safety and regulatory compliance. Knowing exactly where each drug or food item has been ensures that nothing has been tampered with and that medications and the food supply are safe for consumption. The more granular the level of traceability, the better the assurance.
The only way to get down to this granular level is with location tracking that is:
Ubiquitous - location tracking devices that rely on GPS can only track items that are outdoors. Without indoor location tracking, it’s impossible to see where components are in a factory or where inventory is inside a warehouse, for example.
Scalable - the supply chain is spread out across the world - one company may have factories in China and distribution centers in the United States, for example, and they need to be able to maintain an unbroken chain of custody as goods travel across the world. Deploying infrastructure in every location can be prohibitively expensive, so a scalable solution using existing infrastructure is essential.
Precise - it’s essential to track the location down to within a few inches in order to get the necessary granularity. Receiving a wide range of possible locations is less helpful, especially in an extremely large warehouse.
Existing Solutions vs. Deeyook
There are a number of existing real-time location solutions (RTLS) that tend to rely on GPS, Wi-Fi, BLE and other technologies. As evidenced in the image below, these existing solutions are lacking the combination of ubiquity, scalability and precision that is needed. For example, while GPS is extremely precise, it only works where there is reception, which is generally not the case indoors.

Where Deeyook differs is its ability to bring together all three features. Using the existing Wi-Fi infrastructure of 8.5 billion access points (and 1 billion new ones added every year), Deeyook works both indoors and out, and is easily scalable as no additional infrastructure is required.
The solution’s patented technological breakthrough, which combines interferometry and an AI-based physical model, provides a previously unheard of level of precision of 4in.
The Bottom Line
Granular traceability means continuous trackability with no breakage points. When a company is able to continuously track all assets at a super granular level throughout the entire supply chain, they will have an unbroken chain of custody. The constant, real-time visibility enables a whole new level of planning, early identification and remediation of challenges, all of which leads to greater productivity and revenue.
For more information on how to track your assets and improve your chain of custody with Deeyook, please contact us!